Advanced Laser 3D Printing Cells with Meltio Technology
ADDICT3D delivers state-of-the-art laser 3D printing cells powered by the Meltio DED (Directed Energy Deposition) laser head. Whether you’re looking for a fully customized solution or a ready-to-deploy containerized system, we provide the tools to redefine your manufacturing capabilities.
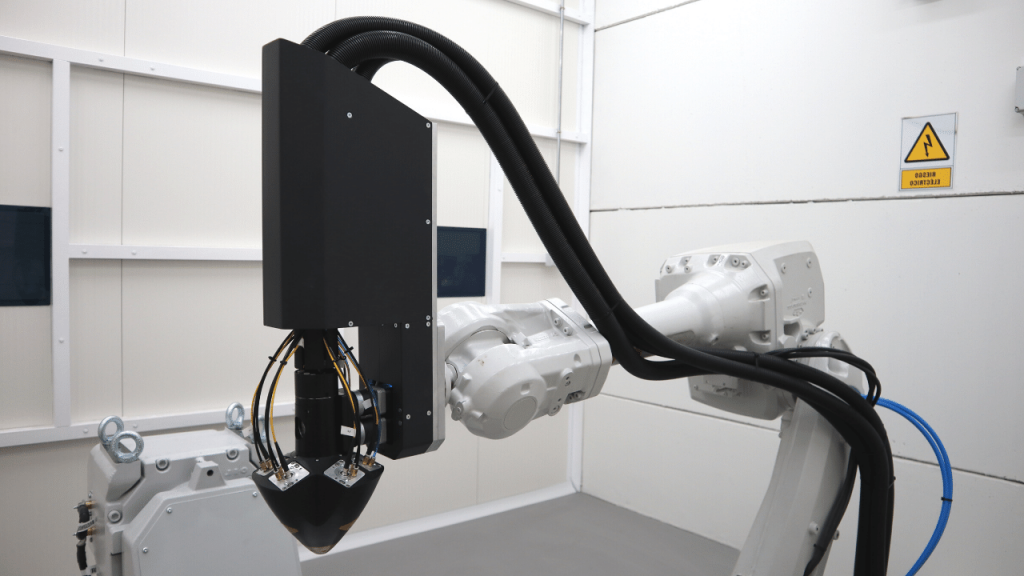
Custom-Designed Printing Cells
Tailored to your specific needs, we build advanced robotic 3D printing cells that seamlessly integrate with your production environment. From compact designs for tight spaces to larger systems for complex manufacturing, our solutions prioritize precision, efficiency, and reliability.
Atratus Printing Cells
For businesses requiring peak design and versatility, our container-style Atratus 3D printing cells offer a plug-and-play solution. This sleek unit bring cutting-edge additive manufacturing capabilities directly to your site, enabling rapid deployment and flexible production.
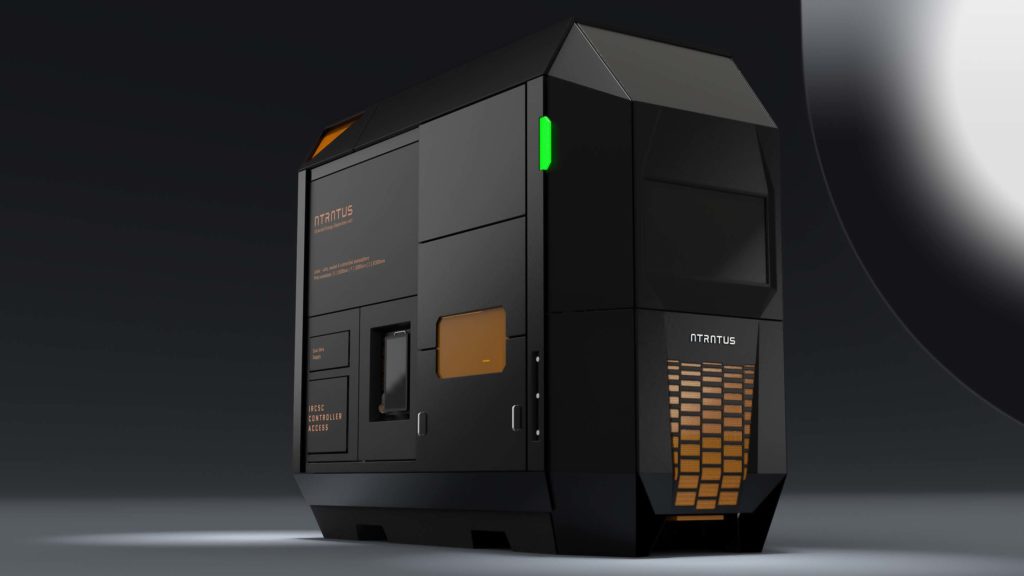
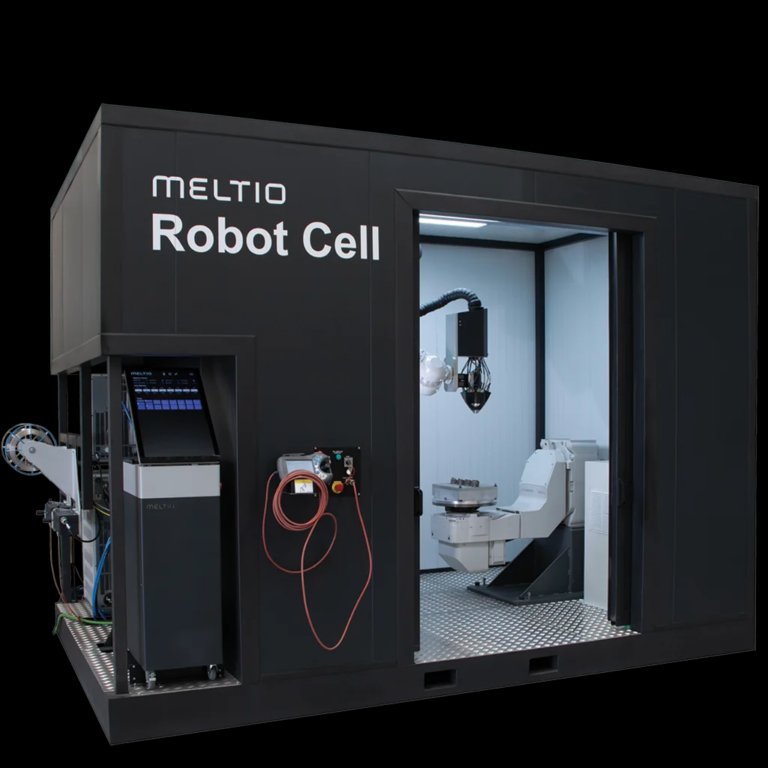
Meltio’s Standard Container Cell Installation
ADDICT3D also provides installation and integration services for Meltio’s standard container cells. Our expertise ensures a smooth implementation process, so you can start leveraging Meltio’s advanced technology with minimal setup time.
Why Meltio DED Technology?
The Meltio DED laser head stands out for its ability to manufacture high-quality metal parts with speed and precision. Its advantages include:
Material Versatility: Print with a variety of metals for diverse applications.
Efficiency: Minimized waste and optimized material usage.
Scalability: Perfect for both prototyping and large-scale production.
High Complexity
Create highly complex parts with infinite degrees of freedom.
Retrofitting
Provide new capability to any robot arm by turning it into a robotic metal printing 3D system.
Part Repair
Cost-effective component repair, part augmentation and feature addition.
Large Size
No inherent constraints when the working envelope is only limited by the size of the robot metal AM motion system.
Open Materials Platform with Wire DED
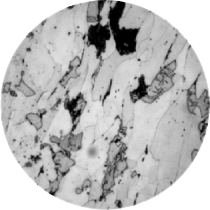
Mild Steels
Cheap and ductile, with unparalleled machinability and weldability.
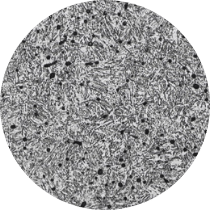
Carbon Steels
High impact strength, retain hardness at high temperatures.
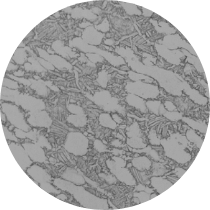
Titanium
High strength to weight ratio and corrosion resistance.
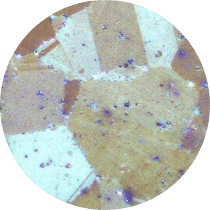
Nickel
High versatility, outstanding heat and corrosion resistance.
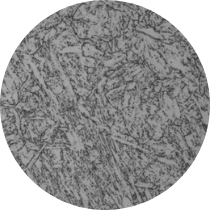
Stainless Steels
Excellent strength and corrosion resistance.
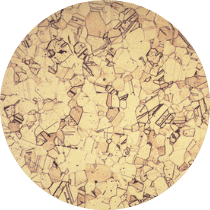
Copper
Under development
Upgrades and Accessories
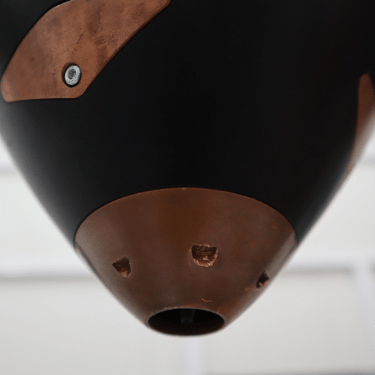
Hot Wire
Programmable power supply that preheats the material to increase the deposition rate of this Wire DED system
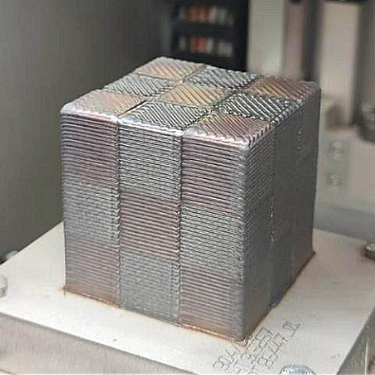
Dual Wire
This option allows to 3D print two wire materials sequentially with very quick wire switches.
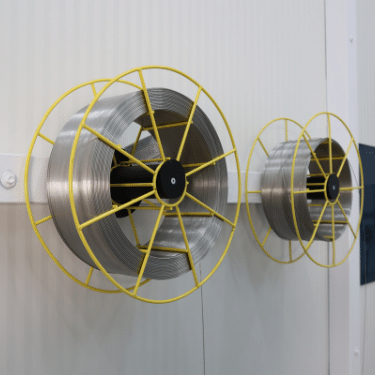
External Wire Drum
Draw from an external wire source. Drums from 100kg may be used for convenience.
Excellent Mechanical Properties
Meltio’s compact heat affected zone process achieves exceptional mechanics, decreased thermal stress and near isotropic properties, exceeding casting and forging material properties.
Part density
Layer Height
Post Processing
Part density
Consistent 99.998% densification
Meltio’s WP-LMD produces fully dense parts with superior microstructure. Exceeding the casting and forging properties, and in certain cases, matching up to wrought material properties.
Layer Height
From 0.3 to 1.2mm layer heights
Meltio’s process allow for an exceptional balance between print speed and surface roughness. Under some conditions, Meltio’s surface roughness using wire can outperform those produced with powder based processes.
Post Processing
Post-process or use as printed
For many applications printed in high-resolution little to no post treatment is necessary. Near net shapes can be post-processed using heat, bead blasting, polishing, brushing or machining.
High Power
Laser power of 1.2kW and optional hot wire system for increased deposition rates.
Extremely Efficient
The wire deposition utilizes 100% of the material and the heat input is kept extremely low making this system a very cost effective 3D metal printing technology
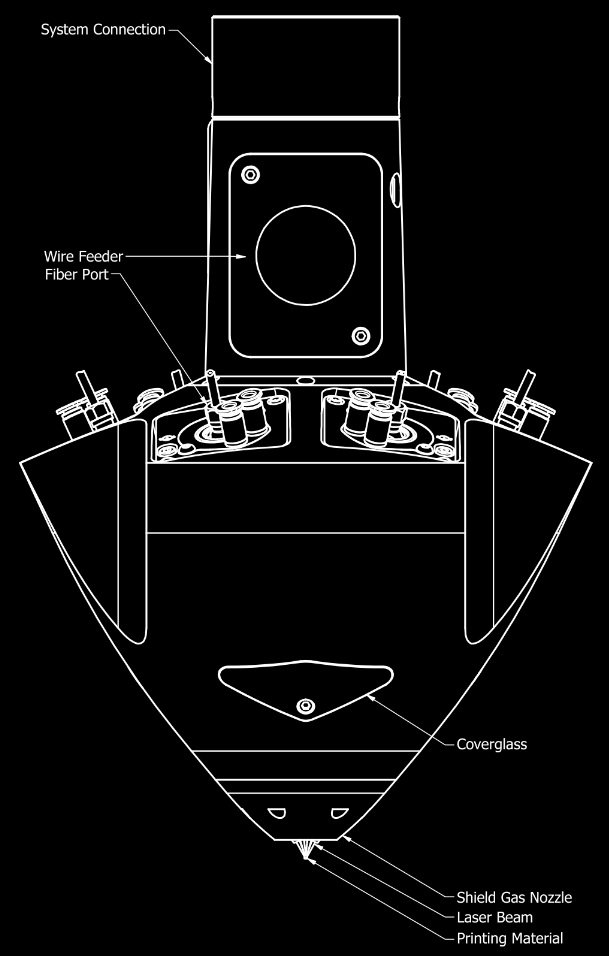